SS904L AISI 904L Stainless Steel (UNS N08904)
Product Introduction
AISI 904L stainless steel (UNS N08904) is a high alloy austenitic stainless steel. Compared with 316L, SS904L has lower carbon (C) content, higher chromium (Cr) content, and approximatively twice the nickel (Ni) and molybdenum (Mo) content of 316L, which makes it have higher high temperature oxidation resistance, pitting resistance, and resistance to reducing acid (eg, sulfuric acid). Nitrogen (N) can reduce the rate of chromium carbide precipitation, thereby reducing the sensitivity of sensitization, it also improve the resistance to pitting and crevice corrosion caused by chlorides. Especially its addition of copper (Cu) makes it useful for all concentrations of sulfuric acid.
Alloy 904L performs better than other austenitic stainless steels due to the higher alloying of nickel and molybdenum. The grade is non-magnetic in all conditions and has excellent formability and weldability. The austenitic structure also gives this grade excellent toughness, even down to cryogenic temperatures The high chromium content promotes and maintains a passive film which protects the material in many corrosive environments. There is no risk of intercrystalline corrosion on cooling or welding due to the low carbon content. Its maximum service temperature is at 450°C. This grade is particularly useful in control and instrumentation tubing applications where 316 and 317L are not suitable.
Alloy 904L was originally developed to withstand environments containing dilute sulfuric acid. It also offers good resistance to other inorganic acids such as hot phosphoric acid as well as most organic acids.
Alloy 904L is easily welded and processed by standard shop fabrication practices.
904L stainless steel (SS904L) is used in petroleum, chemical, fertilizer, marine development towers, tanks, pipes and tubes and heat exchangers. Rolex and other watch manufacturers also use it to make watches
Chemical Requirements
Alloy 904L (UNS NO8904 )
Composition %
C Carbon |
Mn Manganese |
P Phosphorous |
S Sulfur |
Si Silicon |
Ni Nickel |
Cr Chromium |
Mo Molybdenum |
N Nitrogen |
Cu Copper |
0.020 max | 2.00 max | 0.040 max | 0.030 max | 1.00 max | 23.0-28.0 | 19.0-23.0 | 4.0-5.0 | 0.10 max | 1.00-2.00 |
Mechanical Properties | |
Yield Strength | 31 Ksi min |
Tensile Strength | 71 Ksi min |
Elongation(2" min) | 35% |
Hardness(Rockwell B Scale) | 90 HRB max |
Maximum allowable pressure(unit: BAR) | ||||||||
Wall Thickness(mm) | ||||||||
0.89 | 1.24 | 1.65 | 2.11 | 2.77 | 3.96 | 4.78 | ||
O.D(mm) | 6.35 | 393 | 572 | 783 | 1012 | |||
9.53 | 253 | 362 | 499 | 657 | 883 | |||
12.7 | 186 | 265 | 362 | 476 | 646 | |||
19.05 | 172 | 233 | 304 | 410 | ||||
25.4 | 128 | 172 | 223 | 299 | 443 | 549 | ||
31.8 | 136 | 176 | 235 | 345 | 425 | |||
38.1 | 113 | 146 | 194 | 283 | 348 | |||
50.8 | 84 | 108 | 143 | 208 | 255 |
Certificate Of Honor
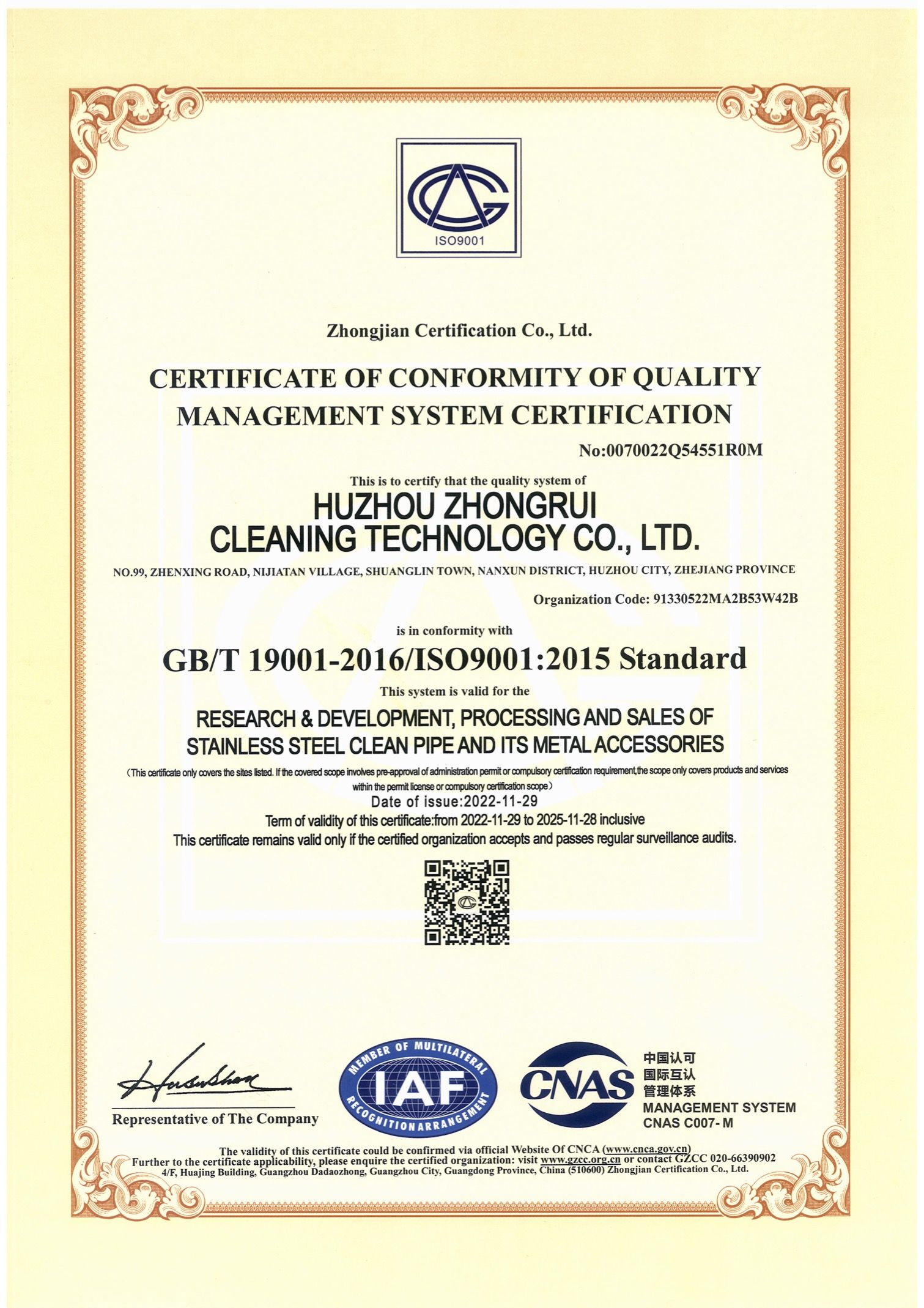
ISO9001/2015 Standard
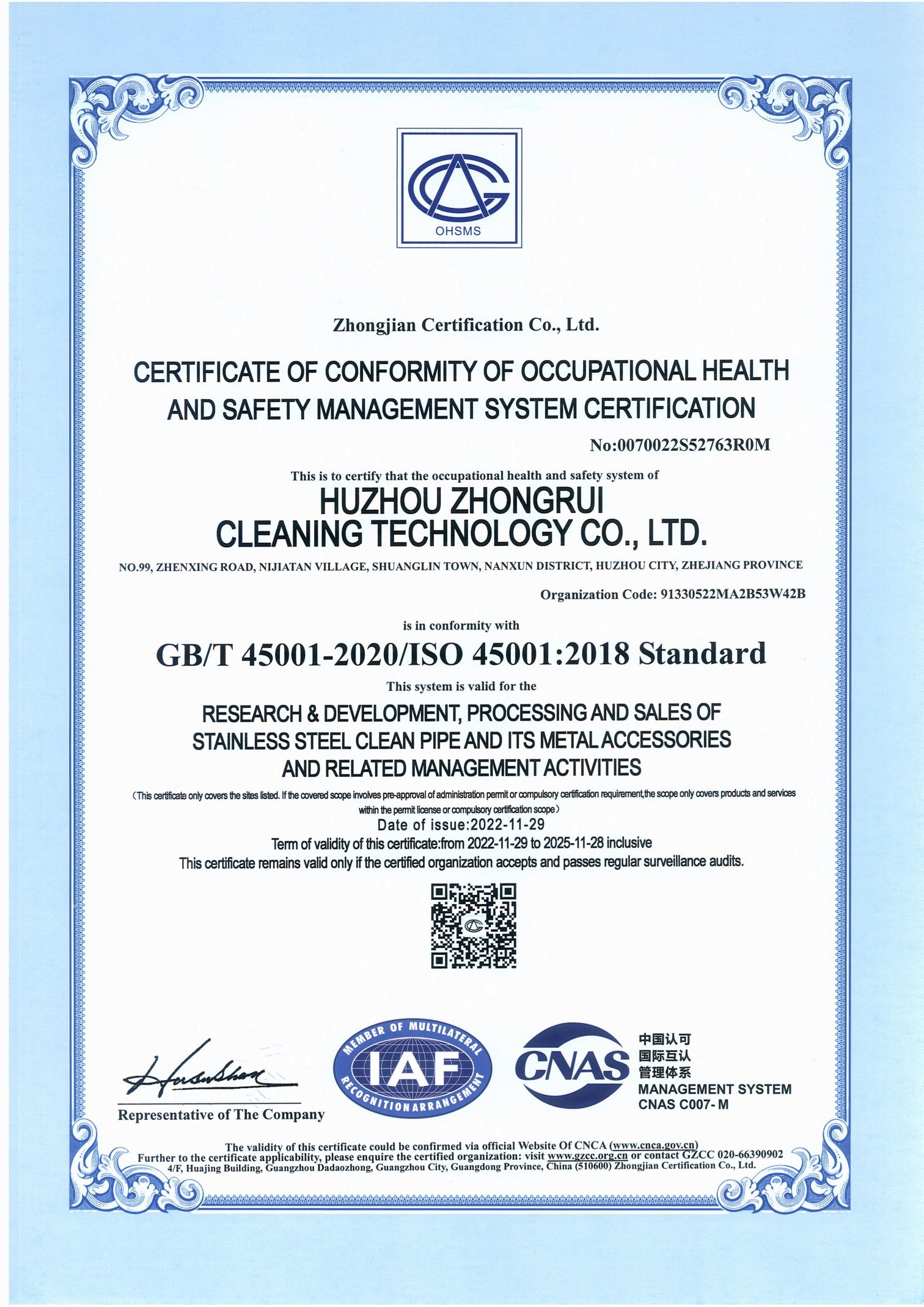
ISO 45001/2018 Standard
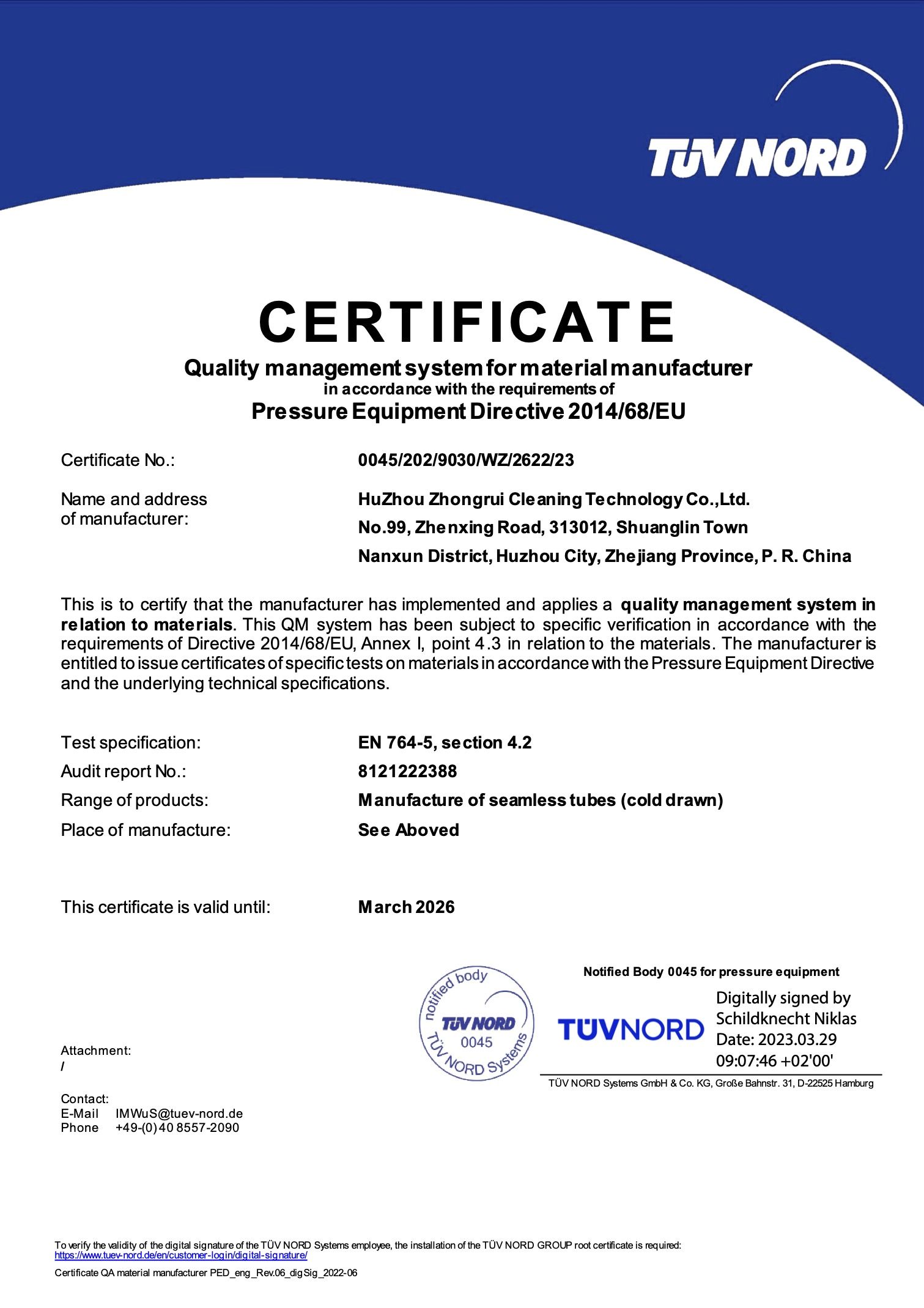
PED Certificate
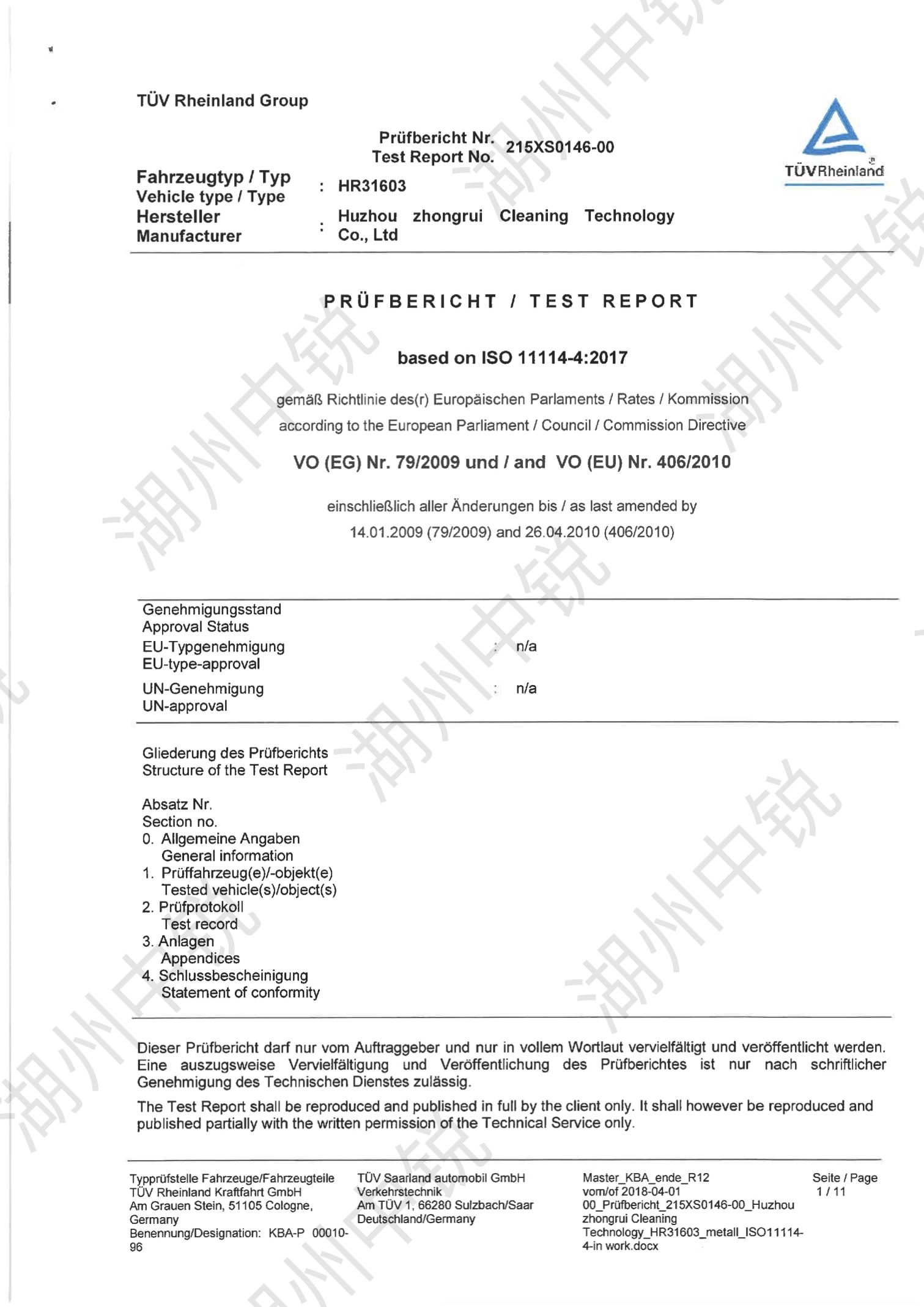
TUV Hydrogen compatibility test certificate
No. | Size(mm) | |
O.D | Thk | |
BA Tube Inner surface roughness Ra0.35 | ||
1/4″ | 6.35 | 0.89 |
6.35 | 1.00 | |
3/8″ | 9.53 | 0.89 |
9.53 | 1.00 | |
1/2” | 12.70 | 0.89 |
12.70 | 1.00 | |
12.70 | 1.24 | |
3/4” | 19.05 | 1.65 |
1 | 25.40 | 1.65 |
BA Tube Inner surface roughness Ra0.6 | ||
1/8″ | 3.175 | 0.71 |
1/4″ | 6.35 | 0.89 |
3/8″ | 9.53 | 0.89 |
9.53 | 1.00 | |
9.53 | 1.24 | |
9.53 | 1.65 | |
9.53 | 2.11 | |
9.53 | 3.18 | |
1/2″ | 12.70 | 0.89 |
12.70 | 1.00 | |
12.70 | 1.24 | |
12.70 | 1.65 | |
12.70 | 2.11 | |
5/8″ | 15.88 | 1.24 |
15.88 | 1.65 | |
3/4″ | 19.05 | 1.24 |
19.05 | 1.65 | |
19.05 | 2.11 | |
1″ | 25.40 | 1.24 |
25.40 | 1.65 | |
25.40 | 2.11 | |
1-1/4″ | 31.75 | 1.65 |
1-1/2″ | 38.10 | 1.65 |
2″ | 50.80 | 1.65 |
10A | 17.30 | 1.20 |
15A | 21.70 | 1.65 |
20A | 27.20 | 1.65 |
25A | 34.00 | 1.65 |
32A | 42.70 | 1.65 |
40A | 48.60 | 1.65 |
50A | 60.50 | 1.65 |
8.00 | 1.00 | |
8.00 | 1.50 | |
10.00 | 1.00 | |
10.00 | 1.50 | |
10.00 | 2.00 | |
12.00 | 1.00 | |
12.00 | 1.50 | |
12.00 | 2.00 | |
14.00 | 1.00 | |
14.00 | 1.50 | |
14.00 | 2.00 | |
15.00 | 1.00 | |
15.00 | 1.50 | |
15.00 | 2.00 | |
16.00 | 1.00 | |
16.00 | 1.50 | |
16.00 | 2.00 | |
18.00 | 1.00 | |
18.00 | 1.50 | |
18.00 | 2.00 | |
19.00 | 1.50 | |
19.00 | 2.00 | |
20.00 | 1.50 | |
20.00 | 2.00 | |
22.00 | 1.50 | |
22.00 | 2.00 | |
25.00 | 2.00 | |
28.00 | 1.50 | |
BA Tube, No request about the inner surface roughness | ||
1/4″ | 6.35 | 0.89 |
6.35 | 1.24 | |
6.35 | 1.65 | |
3/8″ | 9.53 | 0.89 |
9.53 | 1.24 | |
9.53 | 1.65 | |
9.53 | 2.11 | |
1/2″ | 12.70 | 0.89 |
12.70 | 1.24 | |
12.70 | 1.65 | |
12.70 | 2.11 | |
6.00 | 1.00 | |
8.00 | 1.00 | |
10.00 | 1.00 | |
12.00 | 1.00 | |
12.00 | 1.50 |