S32750 Stainless Steel Seamless Tubing
Product Introduction
Super Duplex stainless like S32750, is a mixed microstructure of austenite and ferrite (50/50) which has improved strength over ferritic and austenitic steel grades. The main difference is that Super Duplex has a higher molybdenum and chromium content which gives the material greater Higher chromium also promotes the formation of detrimental intermetallic phases, which are sensitive to 475°C embrittlement because of precipitation of the chromium-rich α’ phase, and to embrittlement by sigma, chi and other phases at higher temperatures.
Alloy 2507 (S32750) also has higher nitrogen content, which not only promotes the formation of austenite and increases the strength, but also delays the formation of intermetallic phases enough to permit processing and fabrication of the duplex grade.
The grade is characterized by very good chloride corrosion resistance, combined with very high mechanical strength. It is particularly suited for use in aggressive environments such as warm chlorinated seawater and acidic chloride-containing media.
Alloy 2507 (S32750) characteristics are as follows:
● Excellent resistance to stress corrosion cracking (SCC) in chloride-bearing environments
● Excellent resistance to pitting and crevice corrosion
● High resistance to general corrosion
● Very high mechanical strength
● Physical properties that offer design advantages
● High resistance to erosion corrosion and corrosion fatigue
● Good weldability
S32750 is designed for demanding applications which require exceptional strength and corrosion resistance, which are found in chemical process, petrochemical, and seawater equipment. It is widely used in offshore oil and gas exploration/production and in heat exchangers in petrochemical/chemical processing. The grade is also suitable for hydraulic and instrumentation applications in tropical marine environments.
Product Specifications
ASTM A-789, ASTM A-790
Chemical Requirements
Super Duplex 2507 (UNS S32750)
Composition %
C Carbon |
Mn Manganese |
P Phosphorous |
S Sulfur |
Si Silicon |
Ni Nickel |
Cr Chromium |
Mo Molybdenum |
N Nitrogen |
Cu Copper |
0.030 max | 1.20 max | 0.035 max | 0.020 max | 0.80 max | 6.0-8.0 | 24.0-26.0 | 3.0-5.0 | 0.24- 0.32 | 0.50 max |
Mechanical Properties | |
Yield Strength | 30 Ksi min |
Tensile Strength | 75 Ksi min |
Elongation(2" min) | 35% |
Hardness(Rockwell B Scale) | 90 HRB max |
Size Tolerance
O.D | O.D Toleracne | W.T Tolerance |
Inch | mm | % |
1/8" | +0.08/-0 | +/-10 |
1/4" | +/-0.10 | +/-10 |
Up to 1/2" | +/-0.13 | +/-15 |
1/2" to 1-1/2" , excl | +/-0.13 | +/-10 |
1-1/2" to 3-1/2" , excl | +/-0.25 | +/-10 |
Note: The tolerance can be negotiated according to the customer's specific requirements |
Maximum allowable pressure(unit: BAR) |
||||||||
Wall Thickness(mm) | ||||||||
0.89 | 1.24 | 1.65 | 2.11 | 2.77 | 3.96 | 4.78 | ||
O.D(mm) | 6.35 | 387 | 562 | 770 | 995 | |||
9.53 | 249 | 356 | 491 | 646 | 868 | |||
12.7 | 183 | 261 | 356 | 468 | 636 | |||
19.05 | 170 | 229 | 299 | 403 | ||||
25.4 | 126 | 169 | 219 | 294 | 436 | 540 | ||
31.8 | 134 | 173 | 231 | 340 | 418 | |||
38.1 | 111 | 143 | 190 | 279 | 342 | |||
50.8 | 83 | 106 | 141 | 205 | 251 |
Certificate Of Honor
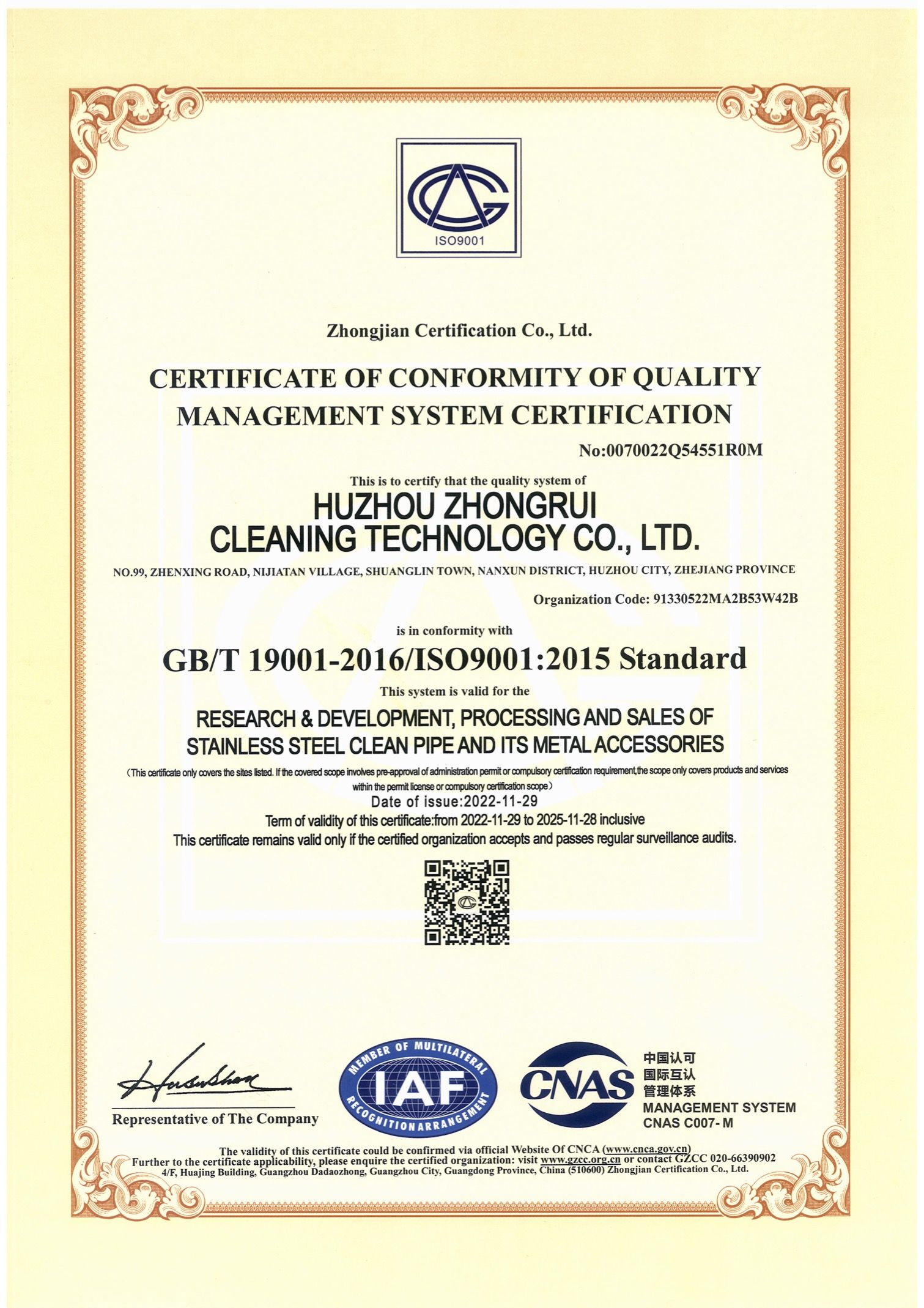
ISO9001/2015 Standard
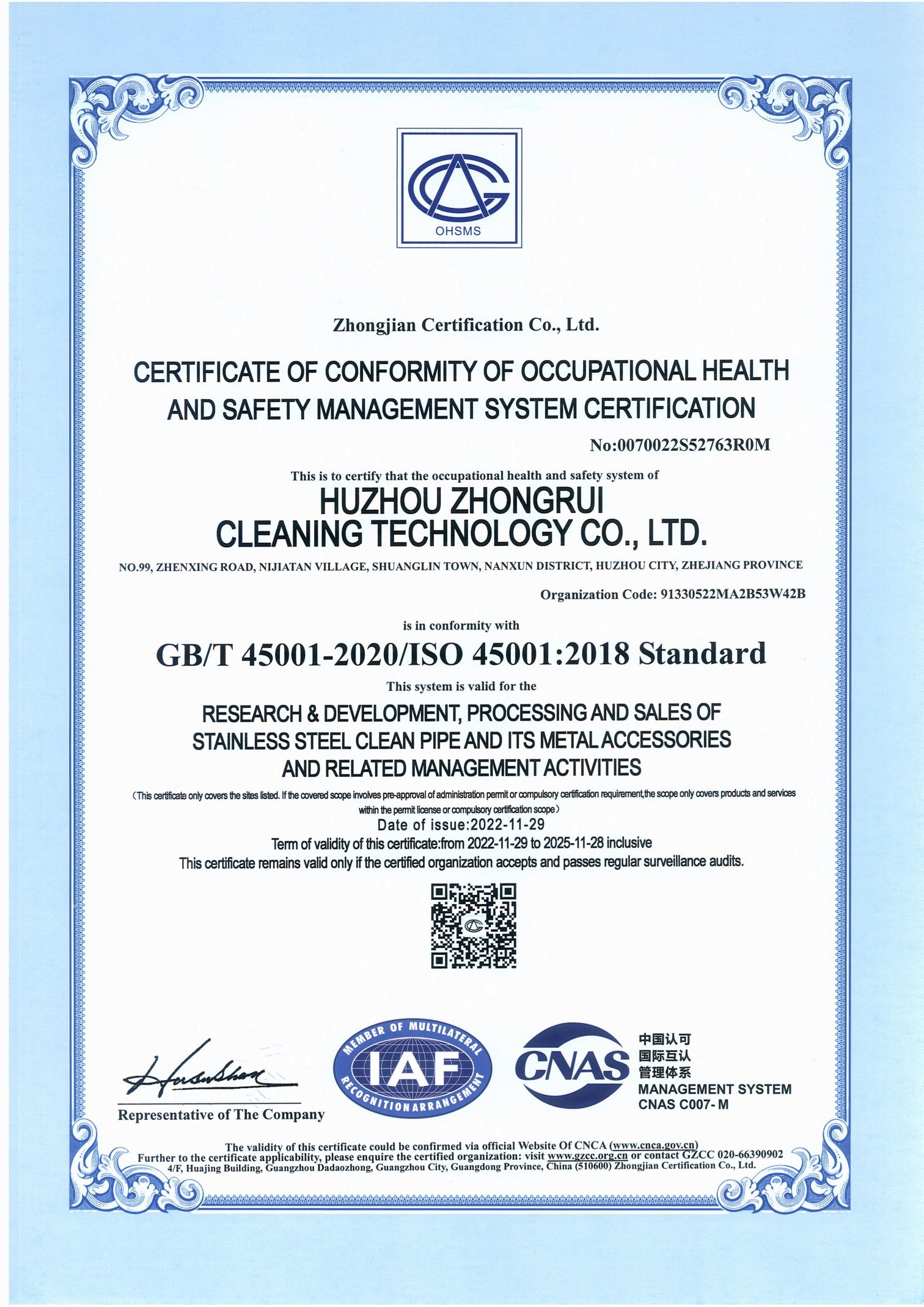
ISO 45001/2018 Standard
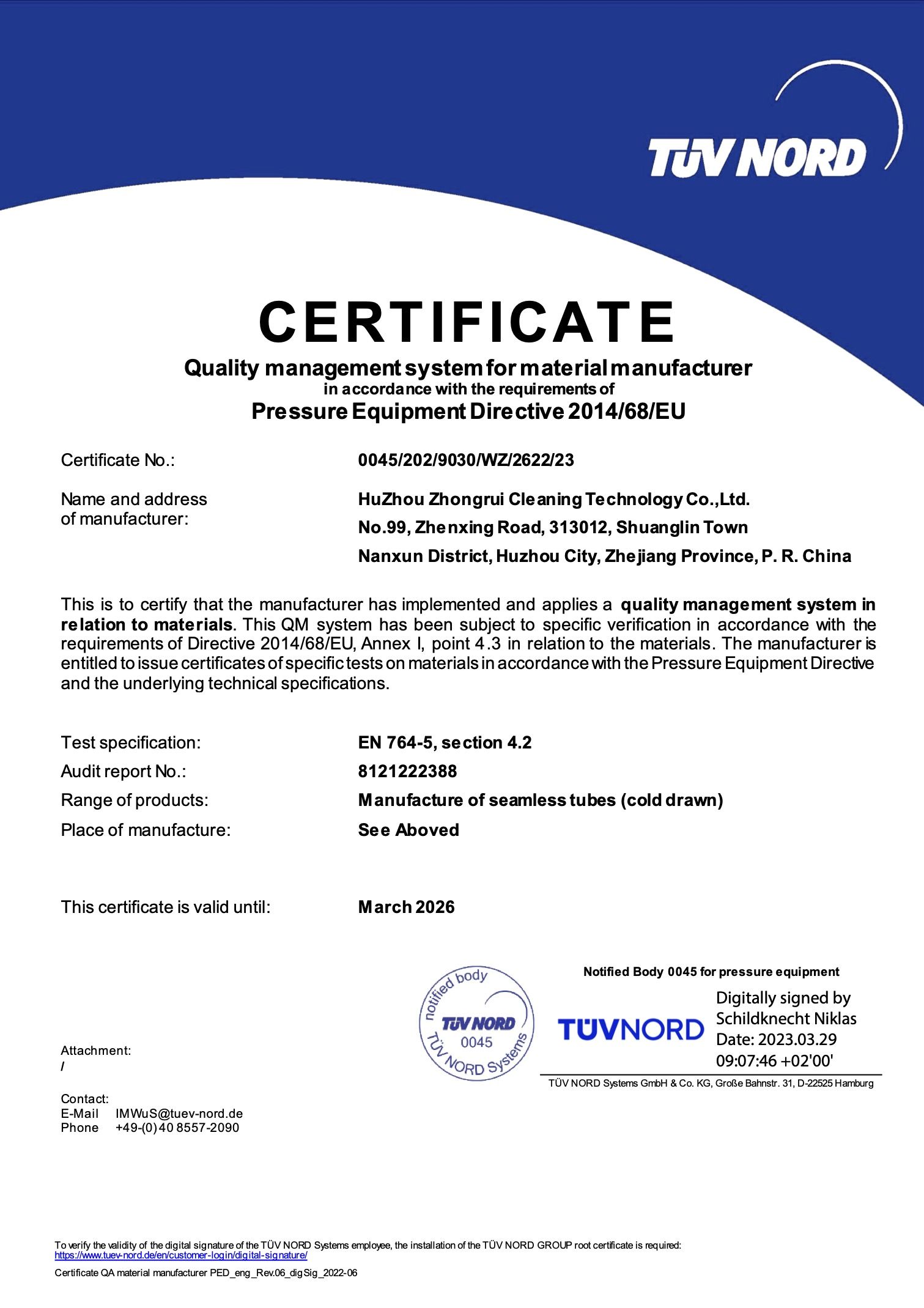
PED Certificate
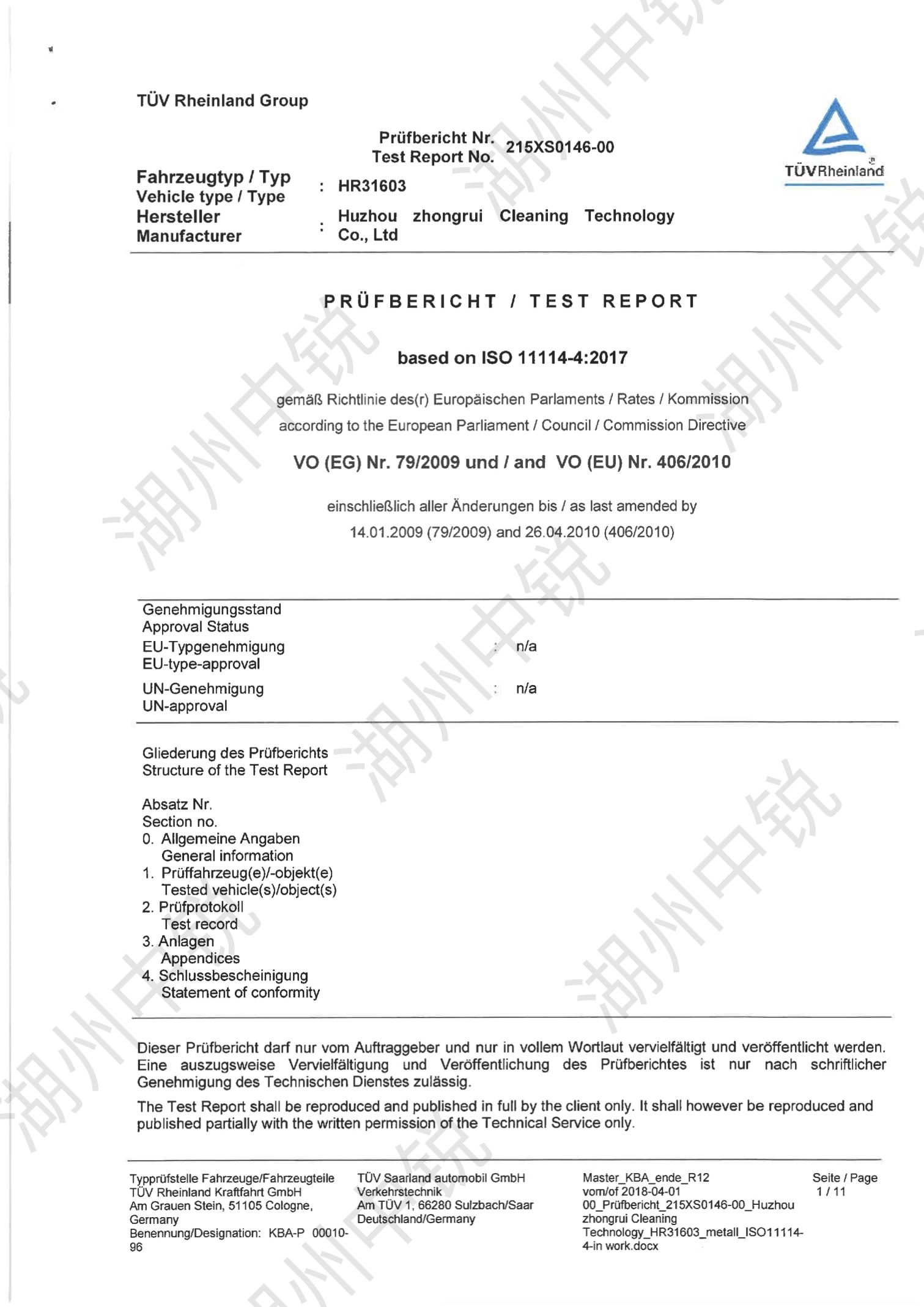
TUV Hydrogen compatibility test certificate
No. | Size(mm) | |
O.D | Thk | |
BA Tube Inner surface roughness Ra0.35 | ||
1/4″ | 6.35 | 0.89 |
6.35 | 1.00 | |
3/8″ | 9.53 | 0.89 |
9.53 | 1.00 | |
1/2” | 12.70 | 0.89 |
12.70 | 1.00 | |
12.70 | 1.24 | |
3/4” | 19.05 | 1.65 |
1 | 25.40 | 1.65 |
BA Tube Inner surface roughness Ra0.6 | ||
1/8″ | 3.175 | 0.71 |
1/4″ | 6.35 | 0.89 |
3/8″ | 9.53 | 0.89 |
9.53 | 1.00 | |
9.53 | 1.24 | |
9.53 | 1.65 | |
9.53 | 2.11 | |
9.53 | 3.18 | |
1/2″ | 12.70 | 0.89 |
12.70 | 1.00 | |
12.70 | 1.24 | |
12.70 | 1.65 | |
12.70 | 2.11 | |
5/8″ | 15.88 | 1.24 |
15.88 | 1.65 | |
3/4″ | 19.05 | 1.24 |
19.05 | 1.65 | |
19.05 | 2.11 | |
1″ | 25.40 | 1.24 |
25.40 | 1.65 | |
25.40 | 2.11 | |
1-1/4″ | 31.75 | 1.65 |
1-1/2″ | 38.10 | 1.65 |
2″ | 50.80 | 1.65 |
10A | 17.30 | 1.20 |
15A | 21.70 | 1.65 |
20A | 27.20 | 1.65 |
25A | 34.00 | 1.65 |
32A | 42.70 | 1.65 |
40A | 48.60 | 1.65 |
50A | 60.50 | 1.65 |
8.00 | 1.00 | |
8.00 | 1.50 | |
10.00 | 1.00 | |
10.00 | 1.50 | |
10.00 | 2.00 | |
12.00 | 1.00 | |
12.00 | 1.50 | |
12.00 | 2.00 | |
14.00 | 1.00 | |
14.00 | 1.50 | |
14.00 | 2.00 | |
15.00 | 1.00 | |
15.00 | 1.50 | |
15.00 | 2.00 | |
16.00 | 1.00 | |
16.00 | 1.50 | |
16.00 | 2.00 | |
18.00 | 1.00 | |
18.00 | 1.50 | |
18.00 | 2.00 | |
19.00 | 1.50 | |
19.00 | 2.00 | |
20.00 | 1.50 | |
20.00 | 2.00 | |
22.00 | 1.50 | |
22.00 | 2.00 | |
25.00 | 2.00 | |
28.00 | 1.50 | |
BA Tube, No request about the inner surface roughness | ||
1/4″ | 6.35 | 0.89 |
6.35 | 1.24 | |
6.35 | 1.65 | |
3/8″ | 9.53 | 0.89 |
9.53 | 1.24 | |
9.53 | 1.65 | |
9.53 | 2.11 | |
1/2″ | 12.70 | 0.89 |
12.70 | 1.24 | |
12.70 | 1.65 | |
12.70 | 2.11 | |
6.00 | 1.00 | |
8.00 | 1.00 | |
10.00 | 1.00 | |
12.00 | 1.00 | |
12.00 | 1.50 |