Instrument tubing is a critical component in a variety of industries that require precise fluid or gas control, such as oil and gas, petrochemical, and power generation. It ensures that fluids or gases are transmitted safely and accurately between instruments, control valves, and measurement devices. These tubes are typically seamless and are designed to withstand high pressures, temperatures, and corrosive environments, making them indispensable for industrial processes.
Instrument tubing is most commonly used in process control systems to transfer pressure, temperature, and flow measurements to gauges, sensors, or control systems. Its primary function is to ensure the integrity and accuracy of the system by preventing leaks or contamination during fluid transmission. These tubes are engineered to be robust, corrosion-resistant, and reliable under extreme conditions, offering long-lasting and maintenance-free performance.

How Instrument Tubing Works in Various Industries
In industries like oil and gas, instrument tubing plays a pivotal role in well monitoring, pressure control, and the transportation of fluids. For example, during the extraction of natural resources, pressure and flow measurements need to be transmitted from the wellhead to control systems that regulate the operation. Without reliable tubing, there is a risk of system failure or inaccurate readings, which could result in costly operational issues.
Similarly, in chemical processing plants, instrument tubing is used to transport corrosive fluids from one part of the system to another. The use of stainless steel 304L tubing in these systems is popular due to its resistance to corrosion from aggressive chemicals and its ability to maintain integrity under high pressure. In these environments, the tubing needs to be robust enough to handle various acids and chemicals, making stainless steel a preferred choice for its durability and corrosion resistance.
In power plants, particularly in nuclear and thermal setups, instrument tubing plays a crucial role in transferring cooling fluids, steam, or gases to control systems that maintain the efficiency and safety of the plant. Materials such as 316L stainless steel are often used due to their ability to withstand the high temperatures and pressures typical of power generation systems.
Benefits of Using High-Quality Instrument Tubing
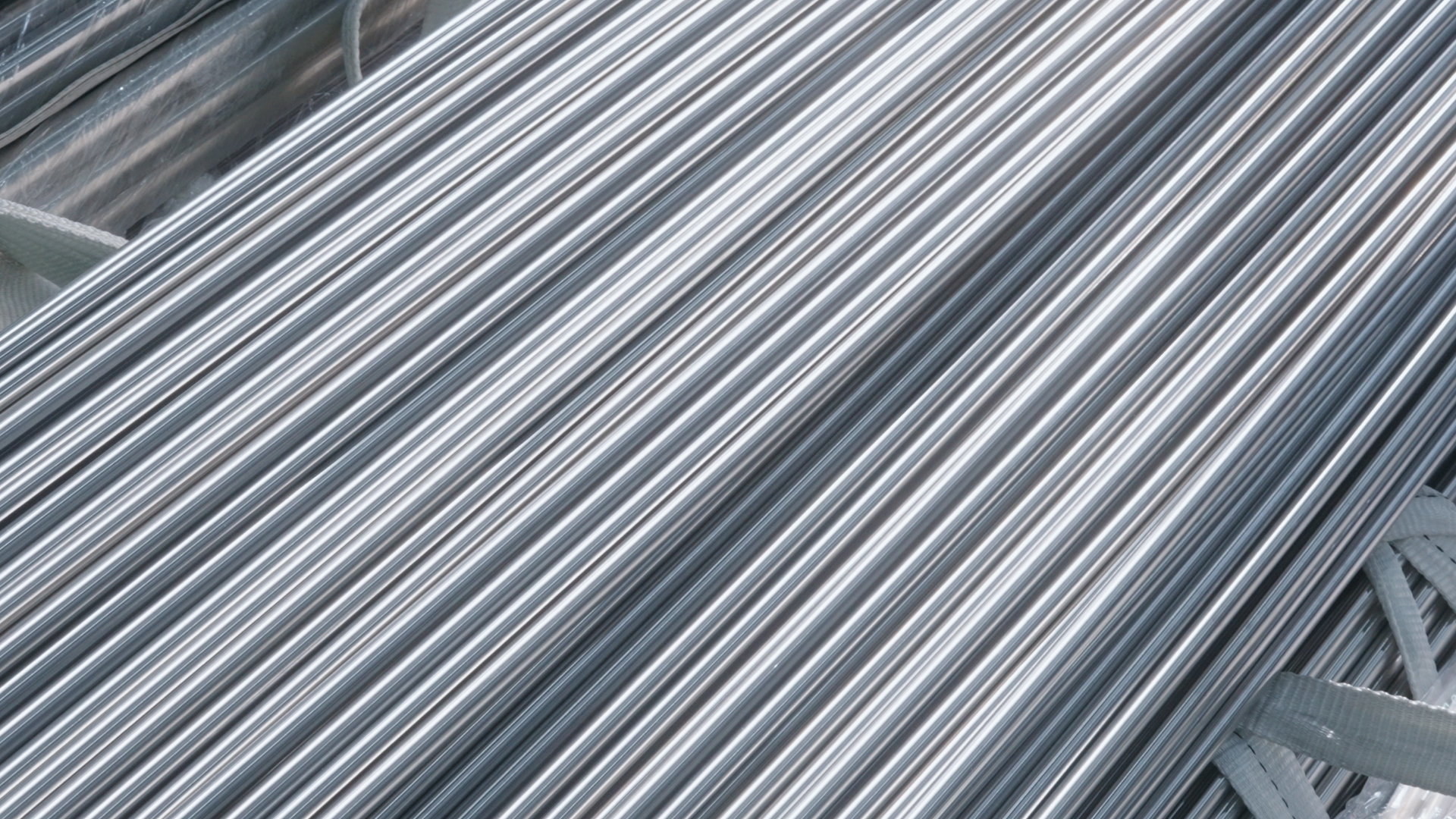
The benefits of using top-quality instrument tubing in industrial systems are numerous. The precision engineering behind these tubes ensures that they can handle:
High Pressure: Tubing is often required to withstand extreme pressure, especially in oil and gas wells or chemical reactors.
Corrosive Environments: Tubing materials like super duplex stainless steel or 304L are chosen for their resistance to corrosion in harsh environments such as those containing chlorides or sulfur compounds.
Temperature Extremes: Instrument tubing must perform reliably in both cryogenic and high-temperature applications, such as in power plants or pharmaceutical environments where sterilization is required.
Instrument tubing is used for transferring not only liquids and gases but also signals. In some cases, the tubing may be connected to pressure transmitters, flow meters, and temperature sensors, playing a vital role in ensuring that industrial processes are tightly controlled and safe. In the pharmaceutical and food industries, stainless steel tubing is favored because it is easy to clean, ensuring sanitary conditions for sensitive processes.
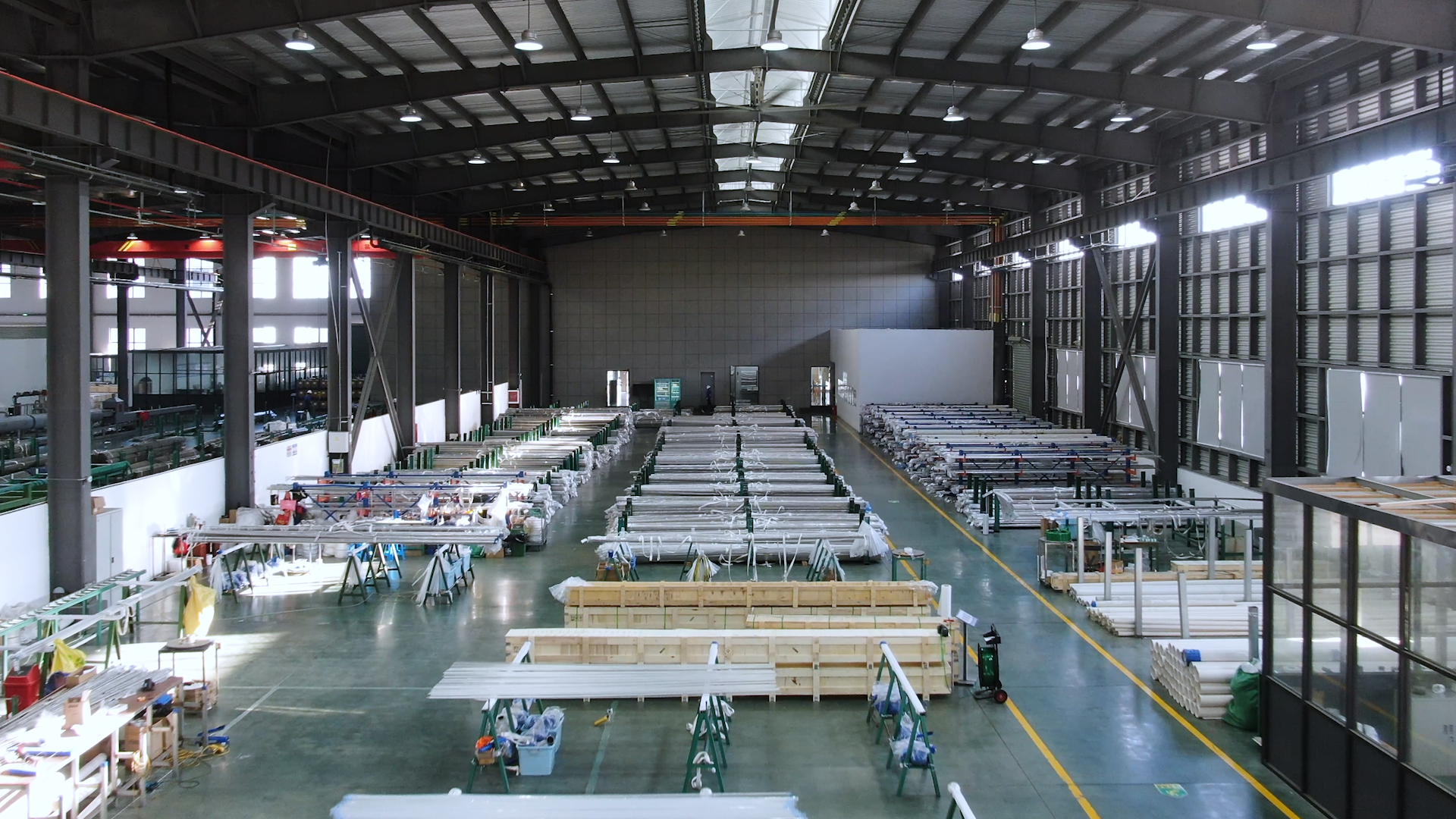
Conclusion
Instrument tubing is a highly specialized form of tubing designed for accurate and reliable transmission of fluids and gases within critical control systems. Industries ranging from oil and gas to pharmaceuticals depend on tubing made from durable materials like 304L stainless steel or 316L to ensure that their operations run smoothly, safely, and efficiently. The precision and reliability of instrument tubing are key to maintaining the integrity of complex systems where even a minor leak or misreading could lead to significant operational challenges
Post time: Jan-07-2025