Monel 400 Alloy (UNS N04400/ W.Nr. 2.4360 and 2.4361 )
Product Introduction
Alloy 400 (UNS N04400) is a solid-solution alloy that can be hardened only by cold working. This nickel-copper chemistry features a high intensity single-phase solid solution metallurgical structure. It has high strength and toughness over a wide temperature range and excellent resistance to many corrosive environments. Monel 400 is one of the few alloys that maintains its strength in sub-zero or cryogenic temperatures.
Alloy 400 has been widely used in applications requiring strong resistance to corrosive environments featuring acids, alkalies, and high temperature steam. especially marine and chemical processing.
As a nickel-copper alloy, alloy 400 has excellent corrosion resistance in a wide variety of media. Alloy 400 is characterized by its general corrosion resistance, good weldability, and moderate to high strength in the tempered conditions. This alloy has excellent resistance to rapidly flowing and warm seawater, brackish water, and steam. It is particularly resistant to hydrochloric and hydrofluoric acids when they are de-aerated. This alloy is slightly magnetic at room temperature. Alloy 400 is widely used in the chemical, oil, and marine engineering industries.
Typical applications are Heat Exchangers, Steam generators, marine fixtures and fasteners, electrical and electronic components, Boiler feedwater heaters, de-aerating heaters, Marine industry and shipbuilding components such as propellers, shafts, fasteners
Alloy 400 may readily be fabricated, machined and joined using standard processes. In general, cold-drawn or cold drawn and stress relieved material provides the best machinability and produces the smoothest finish. All standard welding techniques may be applied to alloy 400. The alloy may also be joined to dissimilar alloys employing appropriate consumables. In addition, joining is possible by brazing or soldering.
Application
Alloy 400 has been widely used in applications requiring strong resistance to corrosive environments featuring acids, alkalies, and high temperature steam. especially marine and chemical processing. Typical applications are Heat Exchangers, Steam generators, marine fixtures and fasteners, electrical and electronic components.
Product Specifications
ASTM B163,ASTM B165
Chemical Requirements
Alloy 400 (UNS N04400)
Composition %
Ni Nickel |
Cu Copper |
Fe lron |
Mn Manganese |
C Carbon |
Si Silicon |
S Sulfur |
63.0 min | 28.0-34.0 | 2.5 max | 2.0 max | 0.3 max | 0.5 max | 0.024 max |
Mechanical Properties | |
Yield Strength | 28 Ksi min |
Tensile Strength | 70 Ksi min |
Elongation(2" min) | 35% |
Size Tolerance
O.D | O.D Toleracne | W.T Tolerance |
Inch | mm | % |
1/8" | +0.08/-0 | +/-10 |
1/4" | +/-0.10 | +/-10 |
Up to 1/2" | +/-0.13 | +/-15 |
1/2" to 1-1/2" , excl | +/-0.13 | +/-10 |
1-1/2" to 3-1/2" , excl | +/-0.25 | +/-10 |
Note: The tolerance can be negotiated according to the customer's specific requirements |
Maximum allowable pressure(unit: BAR) | ||||||||
Wall Thickness(mm) | ||||||||
0.89 | 1.24 | 1.65 | 2.11 | 2.77 | 3.96 | 4.78 | ||
O.D(mm) | 6.35 | 322 | 469 | 642 | 830 | |||
9.53 | 207 | 297 | 409 | 539 | 723 | |||
12.7 | 153 | 217 | 296 | 390 | 530 | |||
19.05 | 141 | 191 | 249 | 336 | ||||
25.4 | 105 | 141 | 183 | 245 | 363 | 450 | ||
31.8 | 111 | 144 | 192 | 283 | 349 | |||
38.1 | 92 | 119 | 159 | 232 | 285 | |||
50.8 | 69 | 89 | 117 | 171 | 209 |
Certificate Of Honor
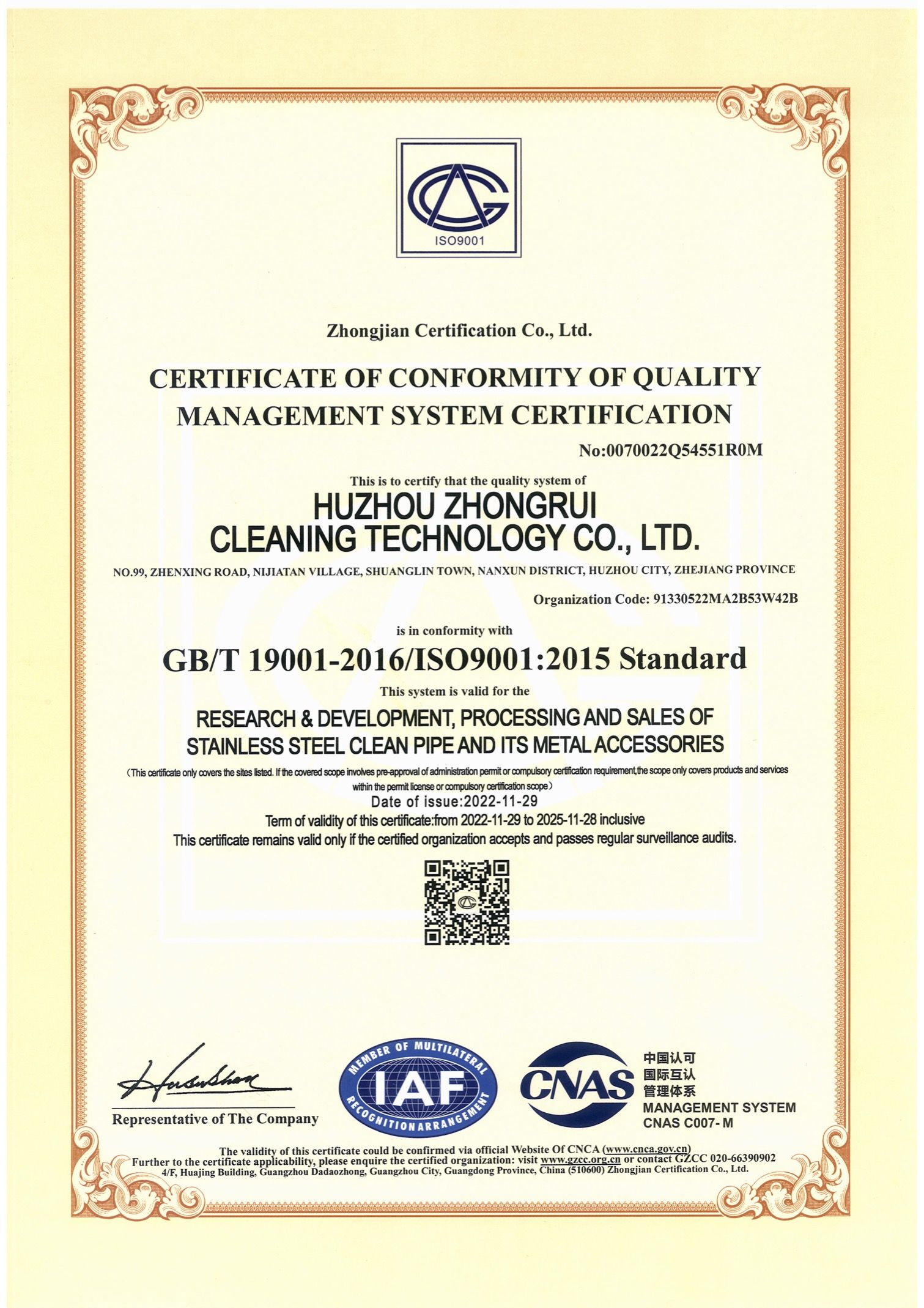
ISO9001/2015 Standard
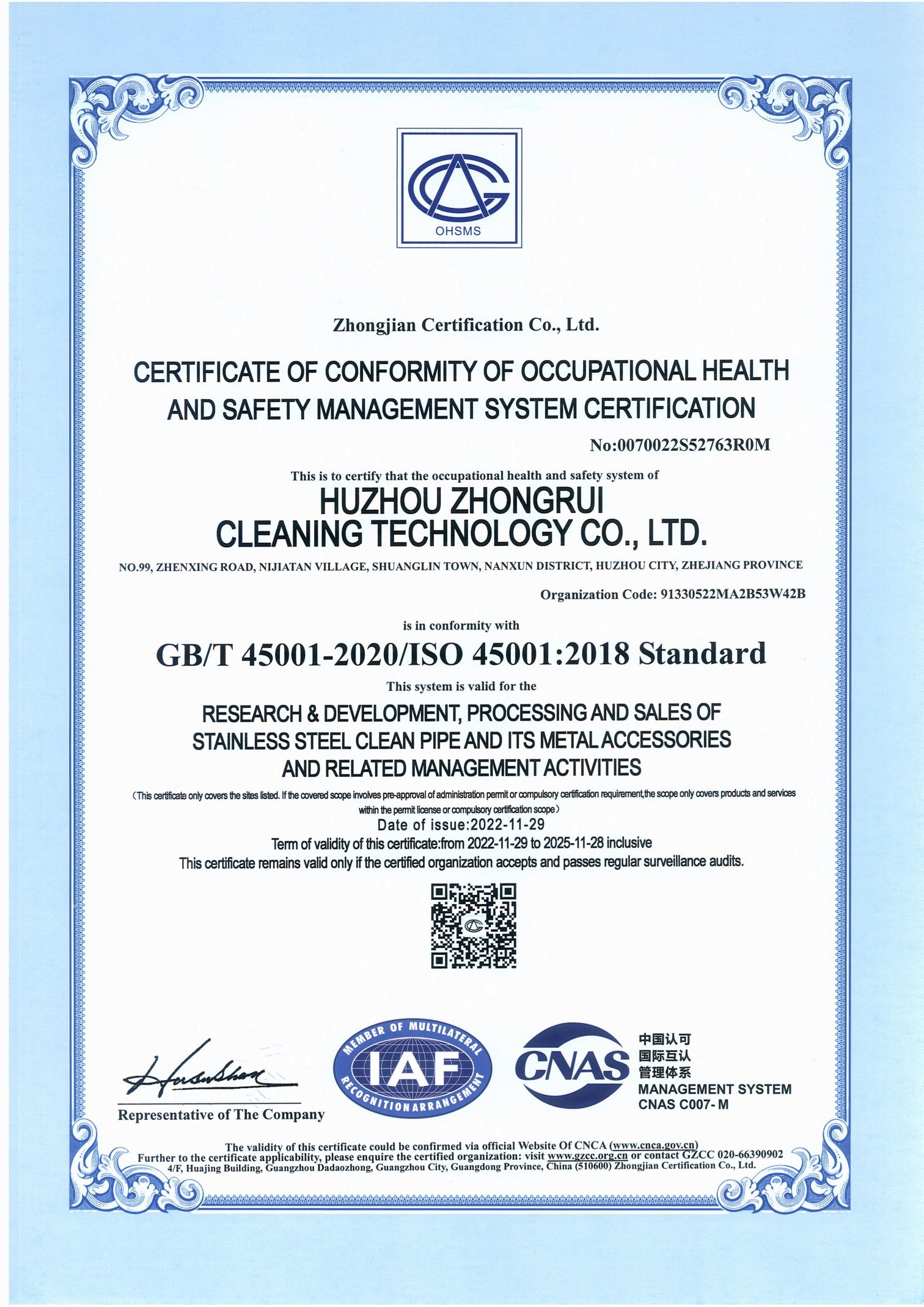
ISO 45001/2018 Standard
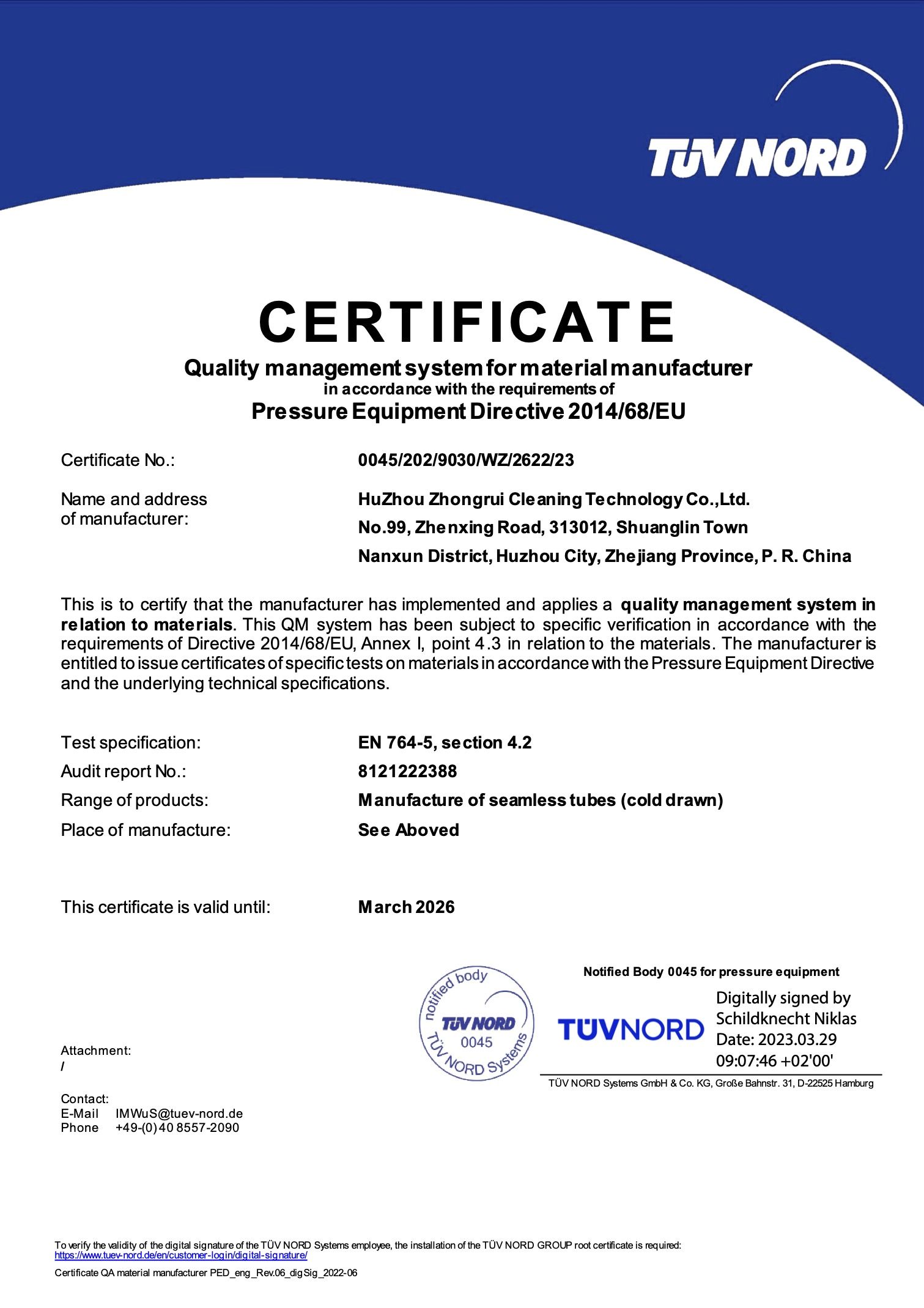
PED Certificate
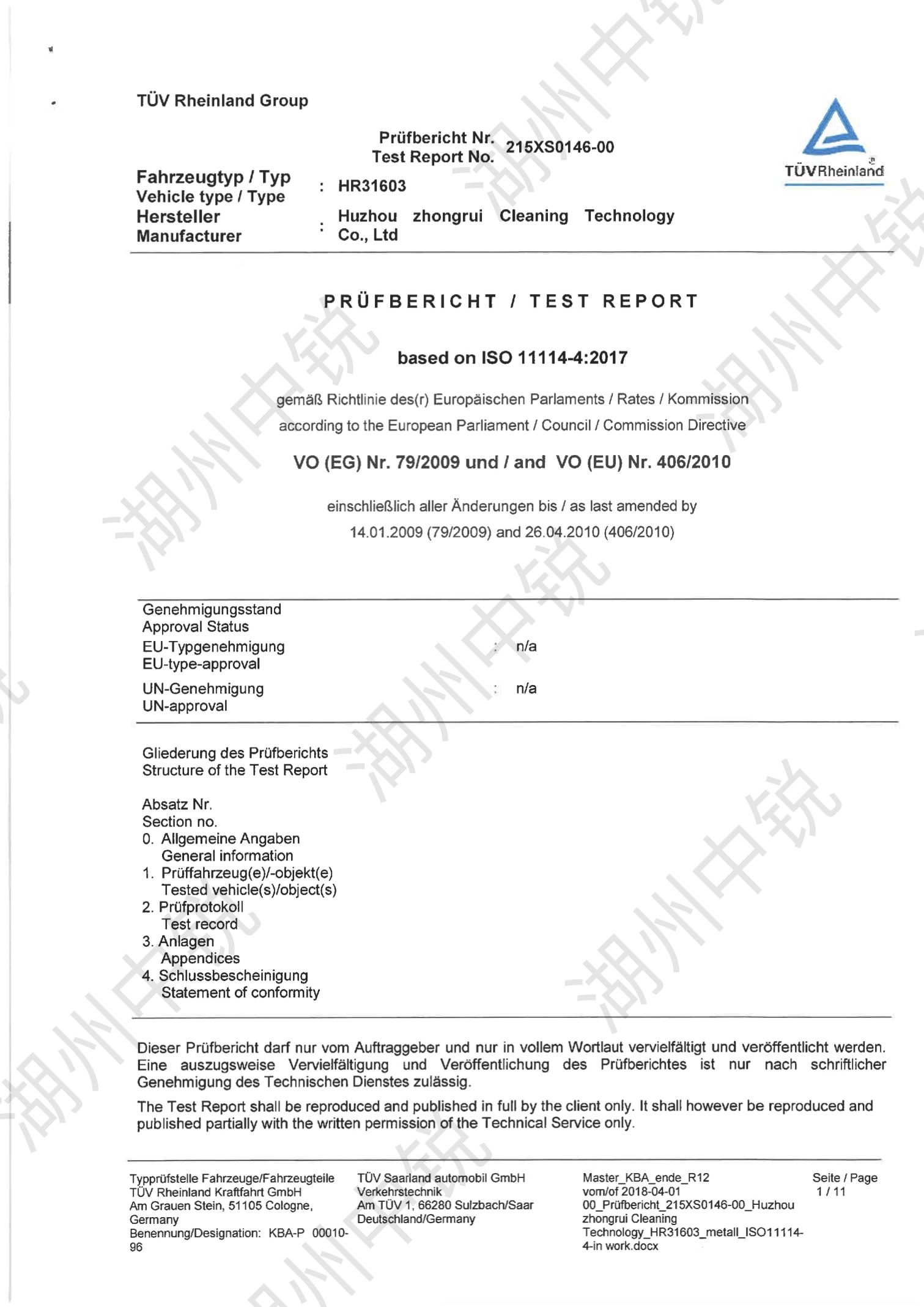
TUV Hydrogen compatibility test certificate
No. | Size(mm) | |
O.D | Thk | |
BA Tube Inner surface roughness Ra0.35 | ||
1/4″ | 6.35 | 0.89 |
6.35 | 1.00 | |
3/8″ | 9.53 | 0.89 |
9.53 | 1.00 | |
1/2” | 12.70 | 0.89 |
12.70 | 1.00 | |
12.70 | 1.24 | |
3/4” | 19.05 | 1.65 |
1 | 25.40 | 1.65 |
BA Tube Inner surface roughness Ra0.6 | ||
1/8″ | 3.175 | 0.71 |
1/4″ | 6.35 | 0.89 |
3/8″ | 9.53 | 0.89 |
9.53 | 1.00 | |
9.53 | 1.24 | |
9.53 | 1.65 | |
9.53 | 2.11 | |
9.53 | 3.18 | |
1/2″ | 12.70 | 0.89 |
12.70 | 1.00 | |
12.70 | 1.24 | |
12.70 | 1.65 | |
12.70 | 2.11 | |
5/8″ | 15.88 | 1.24 |
15.88 | 1.65 | |
3/4″ | 19.05 | 1.24 |
19.05 | 1.65 | |
19.05 | 2.11 | |
1″ | 25.40 | 1.24 |
25.40 | 1.65 | |
25.40 | 2.11 | |
1-1/4″ | 31.75 | 1.65 |
1-1/2″ | 38.10 | 1.65 |
2″ | 50.80 | 1.65 |
10A | 17.30 | 1.20 |
15A | 21.70 | 1.65 |
20A | 27.20 | 1.65 |
25A | 34.00 | 1.65 |
32A | 42.70 | 1.65 |
40A | 48.60 | 1.65 |
50A | 60.50 | 1.65 |
8.00 | 1.00 | |
8.00 | 1.50 | |
10.00 | 1.00 | |
10.00 | 1.50 | |
10.00 | 2.00 | |
12.00 | 1.00 | |
12.00 | 1.50 | |
12.00 | 2.00 | |
14.00 | 1.00 | |
14.00 | 1.50 | |
14.00 | 2.00 | |
15.00 | 1.00 | |
15.00 | 1.50 | |
15.00 | 2.00 | |
16.00 | 1.00 | |
16.00 | 1.50 | |
16.00 | 2.00 | |
18.00 | 1.00 | |
18.00 | 1.50 | |
18.00 | 2.00 | |
19.00 | 1.50 | |
19.00 | 2.00 | |
20.00 | 1.50 | |
20.00 | 2.00 | |
22.00 | 1.50 | |
22.00 | 2.00 | |
25.00 | 2.00 | |
28.00 | 1.50 | |
BA Tube, No request about the inner surface roughness | ||
1/4″ | 6.35 | 0.89 |
6.35 | 1.24 | |
6.35 | 1.65 | |
3/8″ | 9.53 | 0.89 |
9.53 | 1.24 | |
9.53 | 1.65 | |
9.53 | 2.11 | |
1/2″ | 12.70 | 0.89 |
12.70 | 1.24 | |
12.70 | 1.65 | |
12.70 | 2.11 | |
6.00 | 1.00 | |
8.00 | 1.00 | |
10.00 | 1.00 | |
12.00 | 1.00 | |
12.00 | 1.50 |