HASTELLOY C276 (UNS N10276/W.Nr. 2.4819 )
Product Introduction
Alloy C-276 is a nickel-chromium-molybdenum alloy with universal corrosion resistance unmatched by any other alloy. C-276 is also known as Hastelloy C-276 and is an improved wrought version of alloy C in that it usually doesn't need to be solution heat-treated after welding and has vastly improved fabricability.
Alloy C-276 exhibits excellent corrosion resistance in a variety of harsh environments and media. Like many other nickel alloys, it is ductile, easily formed and welded. This alloy is used in most industrial settings where aggressive chemical environments are present and other alloys have failed.
HASTELLOY C276 is a Nickel-chromium-molybdenum wrought alloy that is considered the most versatile corrosion resistant alloy available. This alloy is resistant to the formation of grain boundary precipitates in the weld heat-affected zone, thus making it suitable for most chemical process applications in an as welded condition. Alloy C-276 also has excellent resistance to pitting, stress-corrosion cracking and oxidizing atmospheres up to 1900°F. Alloy C-276 has exceptional resistance to a wide variety of chemical environments.
Alloy C276 showing excellent resistance to mechanical and chemical degradation. The high nickel and molybdenum content impart remarkable corrosion resistance in reducing environments, while chromium provides the same in an oxidizing media. The low carbon contenet minimizes carbide precipitation during welding to maintain corrosion resistance in as-welded structures.
Characteristics
● Superior corrosion resistance.
● Exceptionally low magnetic permeabilty.
● Outstanding cryogenic properties.
● Outstanding corrosion resistance.
Alloy C-276 is frequently used in many industries, including chemical and petrochemical processing, oil and gas, power generation, pharmaceutical, pulp and paper production and waste water treatment. End use applications include stack liners, ducts, dampers, scrubbers, stack gas reheaters, heat exchangers, reaction vessels, evaporators, transfer piping and many other highly corrosive applications.
Product Specifications
ASTM B622
Chemical Requirements
Alloy C276 (UNS N10276)
Composition %
Ni Nickel |
Cr Chromium |
Mo Molybdenum |
Fe lron |
W Tungsten |
C Carbon |
Si Silicon |
Co Cobalt |
Mn Manganese |
V Vanadium |
P PhosphorouS |
S Sulfur |
57.0 min | 14.5-16.5 | 15.0-17.0 | 4.0-7.0 | 3.0-4.5 | 0.010 max | 0.08 max | 2.5 max | 1.0 max | 0.35 max | 0.04 max | 0.03 max |
Mechanical Properties | |
Yield Strength | 41 Ksi min |
Tensile Strength | 100 Ksi min |
Elongation(2" min) | 40% |
Size Tolerance
O.D | O.D Toleracne | W.T Tolerance |
Inch | mm | % |
1/8" | +0.08/-0 | +/-10 |
1/4" | +/-0.10 | +/-10 |
Up to 1/2" | +/-0.13 | +/-15 |
1/2" to 1-1/2" , excl | +/-0.13 | +/-10 |
1-1/2" to 3-1/2" , excl | +/-0.25 | +/-10 |
Note: The tolerance can be negotiated according to the customer's specific requirements |
Maximum allowable pressure(unit: BAR) | ||||||||
Wall Thickness(mm) | ||||||||
0.89 | 1.24 | 1.65 | 2.11 | 2.77 | 3.96 | 4.78 | ||
O.D(mm) | 6.35 | 529 | 769 | 1052 | 1404 | |||
9.53 | 340 | 487 | 671 | 916 | 1186 | |||
12.7 | 250 | 356 | 486 | 664 | 869 | |||
19.05 | 232 | 313 | 423 | 551 | ||||
25.4 | 172 | 231 | 310 | 401 | 596 | 738 | ||
31.8 | 183 | 245 | 315 | 464 | 572 | |||
38.1 | 152 | 202 | 260 | 381 | 468 | |||
50.8 | 113 | 150 | 193 | 280 | 342 |
Certificate Of Honor
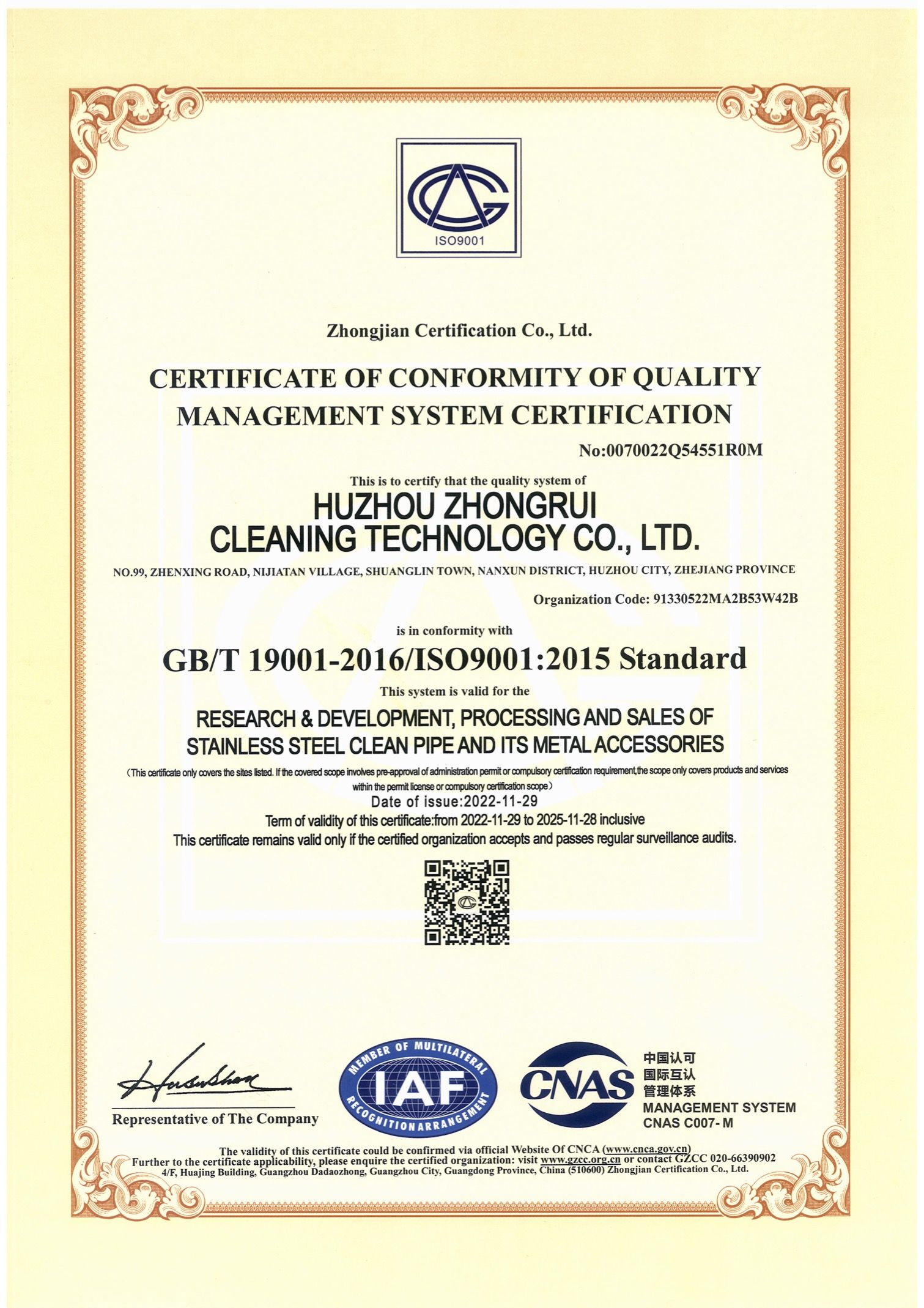
ISO9001/2015 Standard
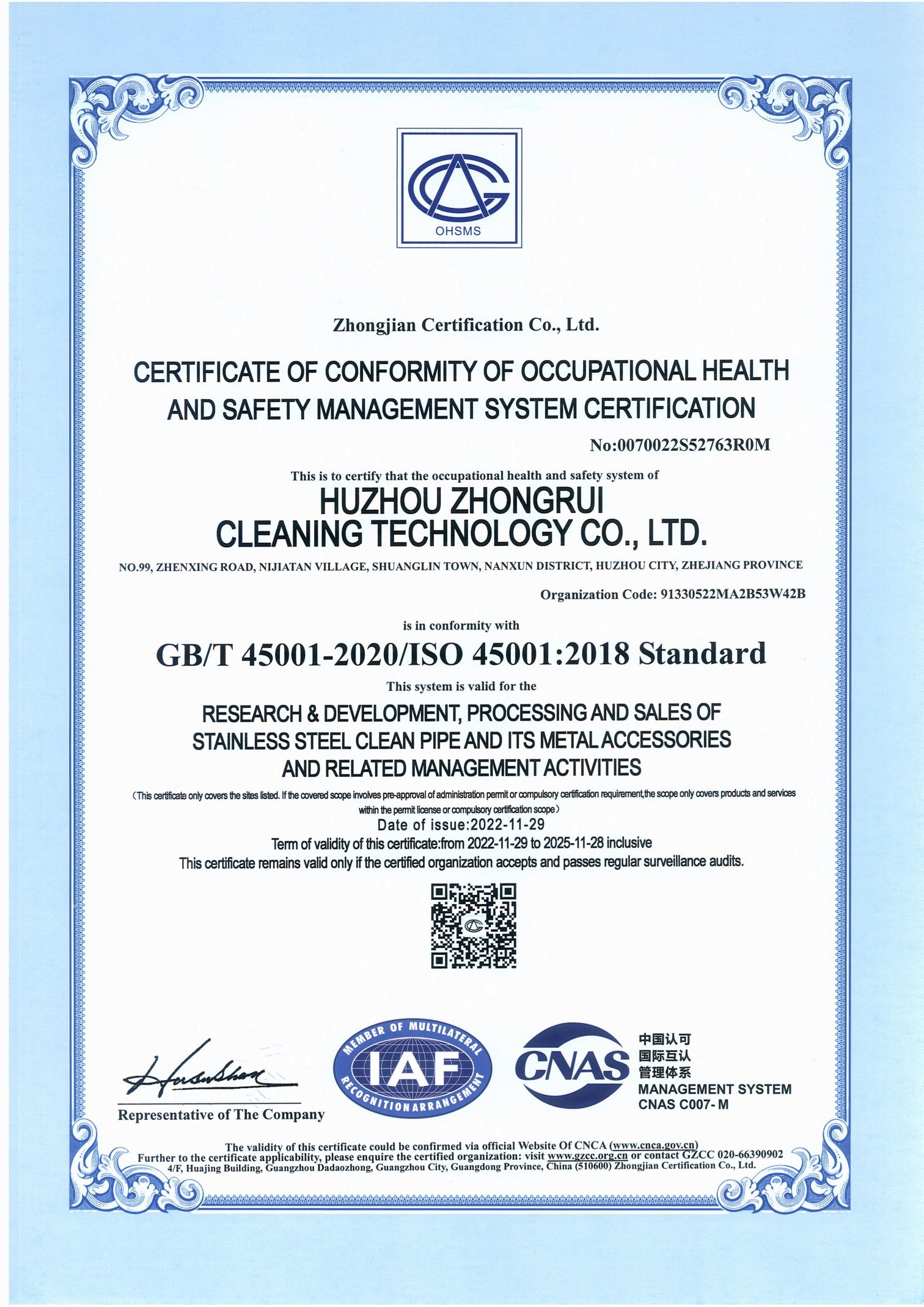
ISO 45001/2018 Standard
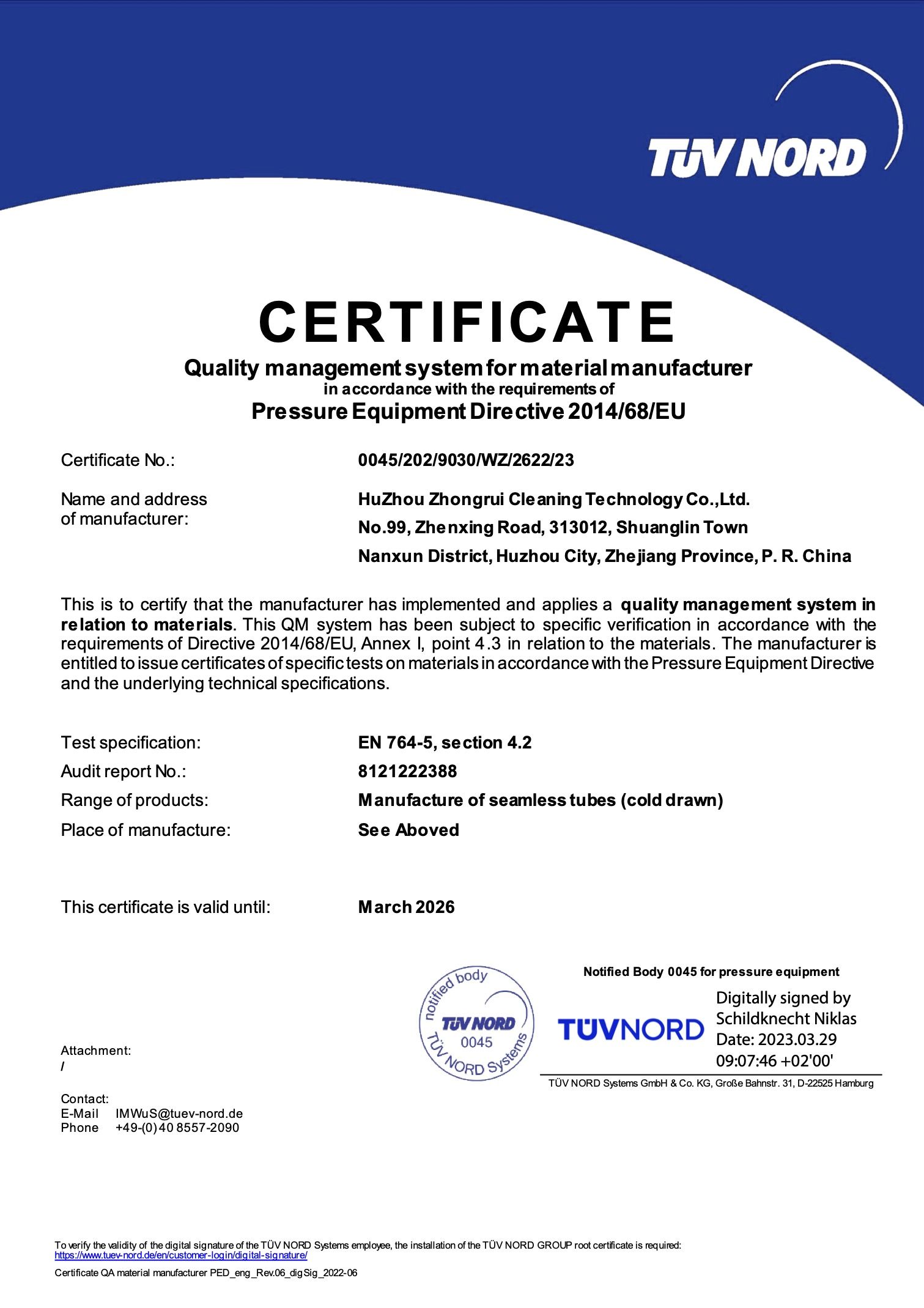
PED Certificate
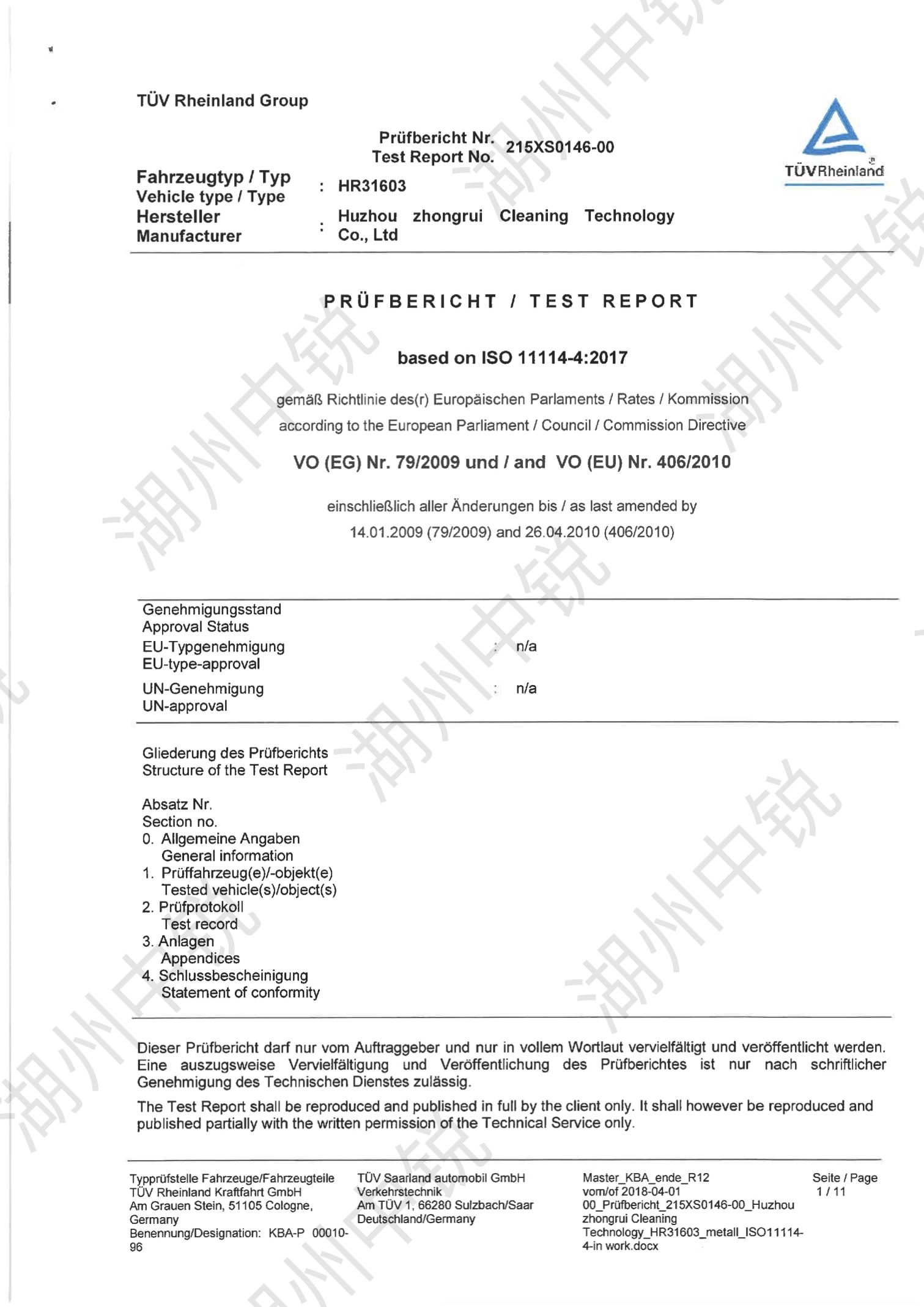
TUV Hydrogen compatibility test certificate
FAQ
INCONEL alloy C-276 (UNS N10276/W.Nr. 2.4819) is known for its corrosion resistance in a wide range of aggressive media. The high molybdenum content imparts resistance to localized corrosion such as pitting.
Both alloys offer comparable corrosion-resisting benefits; however, Inconel has a slight advantage when used in oxidizing applcaitons. On the other hand, as it is more molybdenum forward, Hastelloy offers better performance when subjected to reducing corrosion.
The second difference between alloy c276 and hastelloy c 276 is their temperature tolerance. Alloy c 276 has a maximum operating temperature of 816°C, while hastelloy c 276 has a higher maximum operating temperature of 982°C (1800°F).
FAQ
The short answer is that BPE stands for bioprocessing equipment. The longer answer is that it's the body of standards for bioprocessing equipment developed by the American Society of Mechanical Engineers (ASME), composed of volunteer professionals worldwide in 36 technical sub-fields.
No. | Size(mm) | |
O.D | Thk | |
BA Tube Inner surface roughness Ra0.35 | ||
1/4″ | 6.35 | 0.89 |
6.35 | 1.00 | |
3/8″ | 9.53 | 0.89 |
9.53 | 1.00 | |
1/2” | 12.70 | 0.89 |
12.70 | 1.00 | |
12.70 | 1.24 | |
3/4” | 19.05 | 1.65 |
1 | 25.40 | 1.65 |
BA Tube Inner surface roughness Ra0.6 | ||
1/8″ | 3.175 | 0.71 |
1/4″ | 6.35 | 0.89 |
3/8″ | 9.53 | 0.89 |
9.53 | 1.00 | |
9.53 | 1.24 | |
9.53 | 1.65 | |
9.53 | 2.11 | |
9.53 | 3.18 | |
1/2″ | 12.70 | 0.89 |
12.70 | 1.00 | |
12.70 | 1.24 | |
12.70 | 1.65 | |
12.70 | 2.11 | |
5/8″ | 15.88 | 1.24 |
15.88 | 1.65 | |
3/4″ | 19.05 | 1.24 |
19.05 | 1.65 | |
19.05 | 2.11 | |
1″ | 25.40 | 1.24 |
25.40 | 1.65 | |
25.40 | 2.11 | |
1-1/4″ | 31.75 | 1.65 |
1-1/2″ | 38.10 | 1.65 |
2″ | 50.80 | 1.65 |
10A | 17.30 | 1.20 |
15A | 21.70 | 1.65 |
20A | 27.20 | 1.65 |
25A | 34.00 | 1.65 |
32A | 42.70 | 1.65 |
40A | 48.60 | 1.65 |
50A | 60.50 | 1.65 |
8.00 | 1.00 | |
8.00 | 1.50 | |
10.00 | 1.00 | |
10.00 | 1.50 | |
10.00 | 2.00 | |
12.00 | 1.00 | |
12.00 | 1.50 | |
12.00 | 2.00 | |
14.00 | 1.00 | |
14.00 | 1.50 | |
14.00 | 2.00 | |
15.00 | 1.00 | |
15.00 | 1.50 | |
15.00 | 2.00 | |
16.00 | 1.00 | |
16.00 | 1.50 | |
16.00 | 2.00 | |
18.00 | 1.00 | |
18.00 | 1.50 | |
18.00 | 2.00 | |
19.00 | 1.50 | |
19.00 | 2.00 | |
20.00 | 1.50 | |
20.00 | 2.00 | |
22.00 | 1.50 | |
22.00 | 2.00 | |
25.00 | 2.00 | |
28.00 | 1.50 | |
BA Tube, No request about the inner surface roughness | ||
1/4″ | 6.35 | 0.89 |
6.35 | 1.24 | |
6.35 | 1.65 | |
3/8″ | 9.53 | 0.89 |
9.53 | 1.24 | |
9.53 | 1.65 | |
9.53 | 2.11 | |
1/2″ | 12.70 | 0.89 |
12.70 | 1.24 | |
12.70 | 1.65 | |
12.70 | 2.11 | |
6.00 | 1.00 | |
8.00 | 1.00 | |
10.00 | 1.00 | |
12.00 | 1.00 | |
12.00 | 1.50 |